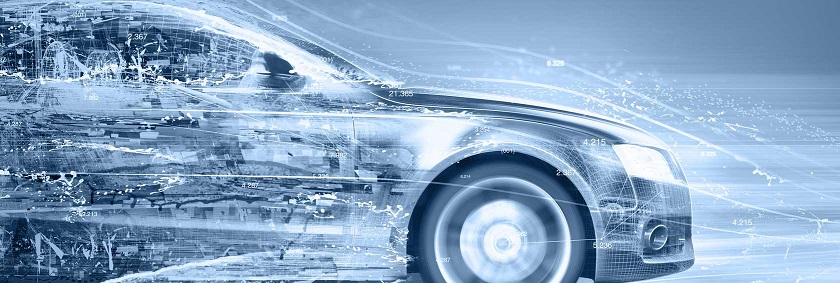
Engine designers are
always looking for alternative ways to reduce costs and emissions and
improve fuel economy and performance. One way to improve automotive
design is through material replacement. Advanced ceramics, like Al2O3 Alumina Ceramics, AlN Aluminium Nitride Ceramics,Si3N4 Silicon Nitride Ceramics, ZrO2 Zirconia Ceramics, can be used as a technology for many of the key components of future
engines because of their unique heat resistance, wear and corrosion
resistance, light weight, and electrical insulation and thermal
insulation/conductivity.
Advanced ceramics have played an important role in automobiles since the beginning, mainly for spark plug insulators and glass windows. Almost all catalytic converters in modern automobiles have ceramic honeycomb carriers for catalysts, which is very useful in reducing vehicle exhaust emissions. Most modern cars also use ceramic oxygen sensors along with computer controls to optimize combustion and reduce exhaust emissions.
Computer control and other electronic devices in automobiles use a large number of Ceramic Substrates (Alumina Substrates & Aluminium Nitride Substrates) and are critical to the performance of the device. In addition, many electric motors are used in modern automobiles to automatically adjust seat windows and the like, and ceramic magnets are used in many of these motors. Ceramic components are also introduced into the fuel system and valve train of heavy duty diesel engines.
Future vehicles may use ceramics in internal engine structural components, in wear-resistant applications of fuel systems, accessory components in valve systems, such as valves and valve seats. Ceramic fuel cells can also be used in driverless cars in the future.